The Pā at the University of Waikato is one of the more unique commercial projects contractor Hawkins has worked on, from navigating Covid-19 lockdowns to using some of the largest glulam timber beams ever engineered in New Zealand.
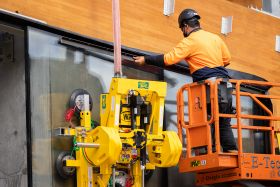
The team even developed a bespoke drill for the job that requires two staff to operate driving the 22,000 screws into the 12,000 fixings that join the building seamlessly together.
Hawkins’ Project Manager, Steve Tapalaga, says the complexity of The Pā build is extremely specialised and has utilised the Hawkins team expertise. From some of the largest windows ever handled in New Zealand to the development of a bespoke drill to drive 22,000 screws into 12,000 fixings, The Pā has been a unique project.
Engineered beams
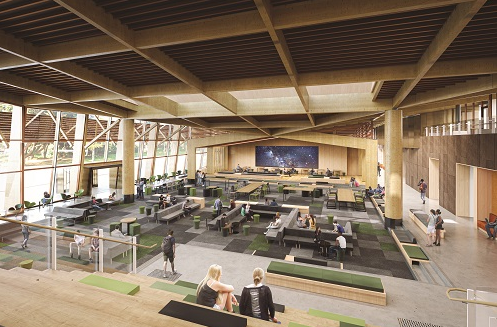
An artist's render of the finished student hub showing where around 200 square metres of the building’s roof converge at one point before the stage.
Engineered wooden glulam beams are joined almost invisibly to give the building its unique form externally, and they are exposed inside the building, to create visual impact.
The project brings concrete, steel, and wood together in a flawless finish that hides almost everything except for the beams.
The best example is above the stage in the Student Hub, where around 200 square metres of the building’s roof converge at one point.
A large piece of steel about one metre long and one metre deep sits, huge rods extending into the glulam beams, holding the load together.
The method
“It’s a beautiful piece of structural engineering. The steel is concealed to the eye. We spent many hours modelling this to ensure all you could see was the striking timber,” says Steve Tapalaga.
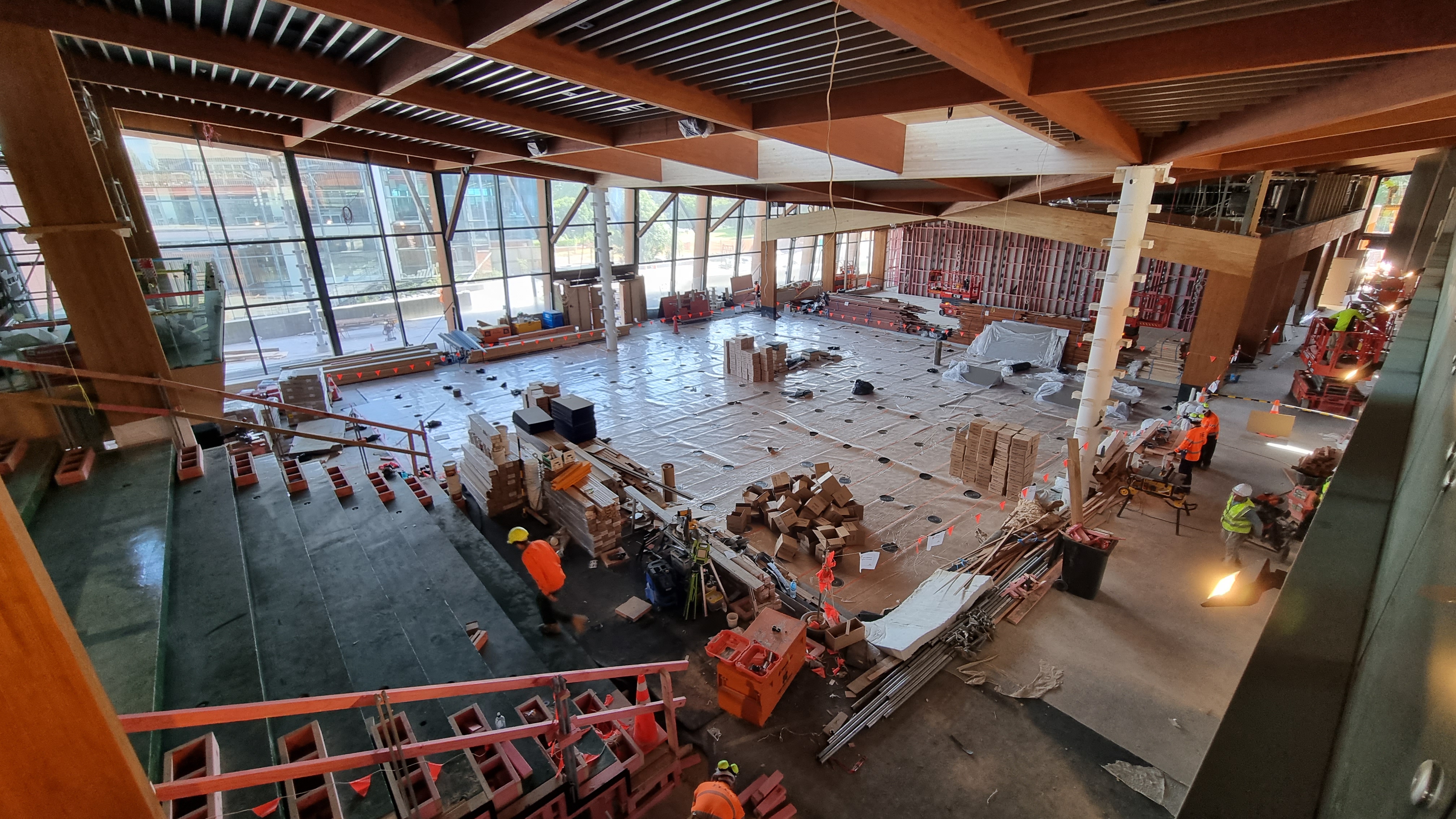
Construction of the Student Hub area, February 2023.
The wood is joined using mortise and tenon joints, a method used for thousands of years to join pieces of wood, but seldom, if ever, on this scale for commercial construction in New Zealand.
Slots are created in the timber where steel rods are inserted to hold them together, all out of view of the naked eye and with millimetre tolerances.
“In a typical construction you can manipulate steel columns and move them horizontally and laterally to get things to line up but when you have 30 metre pieces of timber more than one metre thick and you’re trying to land them all together at a single point, you don’t get that kind of play,” says Steve.
He says structural glulam timber has been used in residential and smaller scale projects around New Zealand but never on the scale of The Pā.
A bespoke job
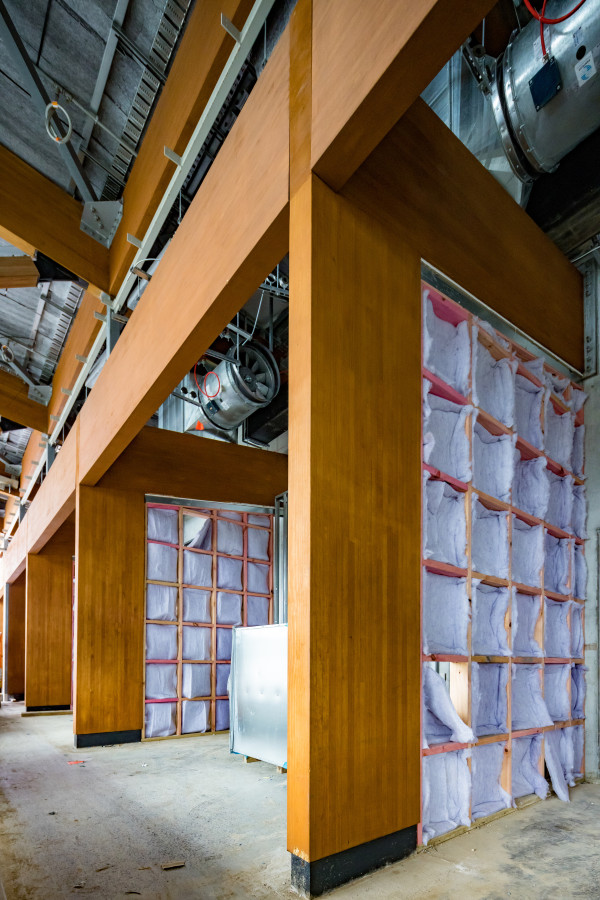
The timber beams had to be carefully managed throughout the construction. Construction photo August 2022.
“There are not a lot of people who have the skill and knowledge on how to put these buildings together in the country," says Steve.
"In New Zealand we grow pine and it’s considered a renewable resource. As we move to longer term environmentally sustainable construction, we will likely see an increase in utilising this kind of method and material” says Steve.
To do the job they designed a bespoke drill that can pierce through the metal plates attached to the wooden glulam beams that hold the building together.
It took three different prototypes and the force needed to drive the screws required two team members to operate the drill. Each of the 22,000 screws took about two minutes to fix in place.
The timber beams have also had to be carefully managed throughout the construction.
“The beams arrived to site at the start of the construction in the dirty and dusty phase. Due to the exposure of the timber within the completed design, we had to protect them throughout,” says Steve.
They were wrapped with protective material to prevent dings and scratches, but the team also had to be careful where and when the wrapping was in place, so the beams didn’t discolour with sun and weather exposure.
A big job
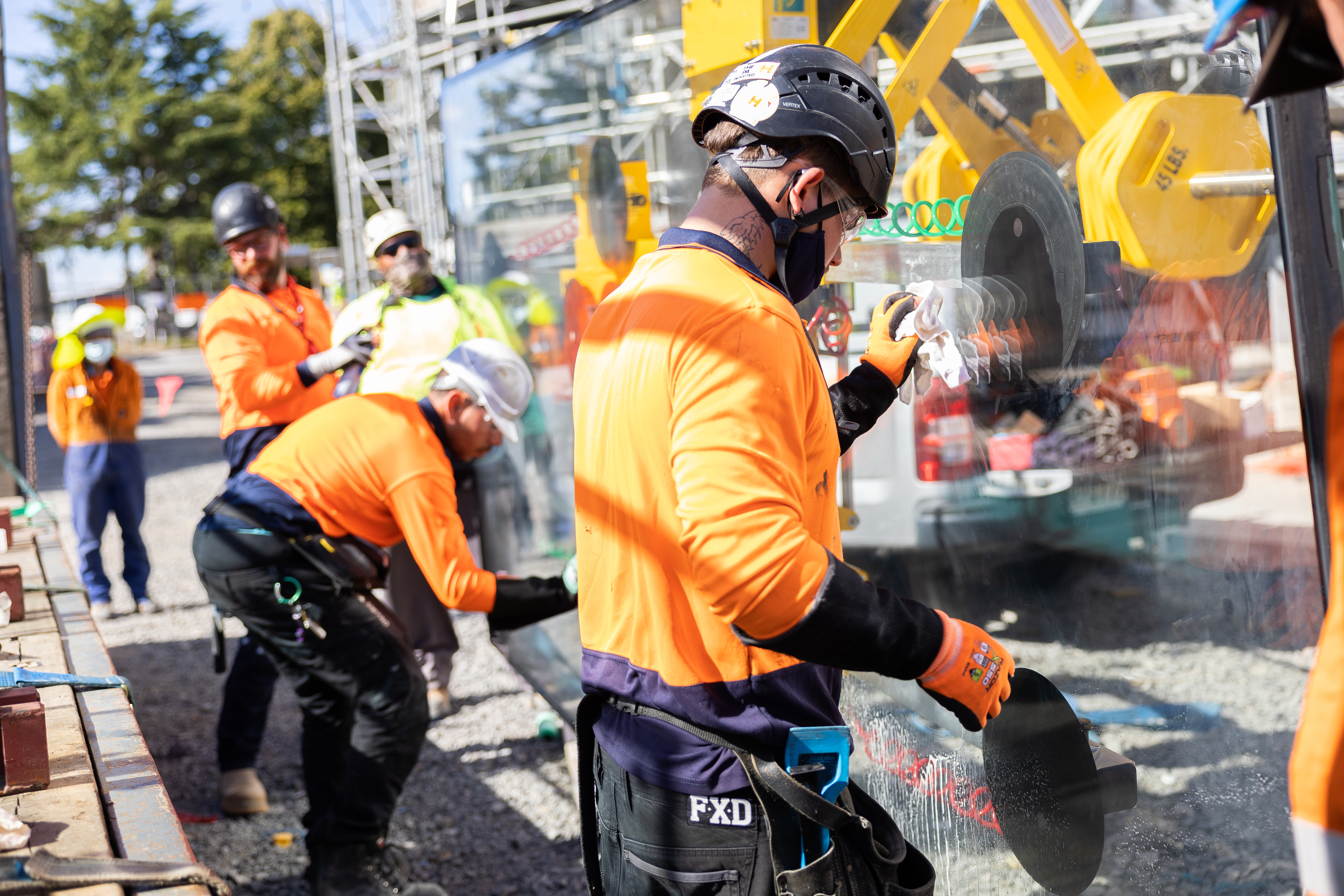
Around 120 staff have been on site during the project which has also employed about 88 subcontractors including businesses like Wight Aluminium and Metro Glass who designed the bespoke windows.
Around 120 staff have been on site during the project and at the end of June 2022 they had worked 300,000 hours. The project has also employed about 88 subcontractors, many of them locally, helping to support the local economy, says Steve.
Covid-19 and lockdowns have proved a challenge throughout the build he says.
“Covid has certainly had a significant impact on the project and it’s not just the resources side of it and having staff available, but material availability and scarcity too,” says Steve.
“One of the weirdest things we were chasing around the country for was paint hardener which we never would have thought would have been hard to source. Another was pan head screws.”
He says they worked closely with the University to ensure there was space on campus to store material so they could bulk order what was needed. Construction staff were even put up in student accommodation so they could continue working during Covid-19 lockdowns when students weren’t using the facilities.
“I’m immensely proud of what our team and subcontractors have created. It’s not your usual project and it’s also been built during a time that’s not business as usual. I think the level of finish that has been achieved is outstanding. It will be iconic to the University.”